A Process Efficiency Case Study
As companies focus on growing profitability, it is increasingly important to take advantage of the latest products and services to maximize efficiencies. While new projects are often easier from a timing, funding, and validation standpoint to implement new innovative technologies that positively impact efficiency, often there are significant gains to be realized by analyzing and improving existing, well established processes. The benefits can be rewarding to management, the employees, and the shareholders from a fiscal, ergonomic, or safety standpoint. It takes a committed Manager, willing to expose the gaps in their process to make the necessary investment to evaluate effective solutions.
The following is a case study of how an investment in innovative equipment technologies can improve process efficiency, remove safety risks, and increase overall profitability.
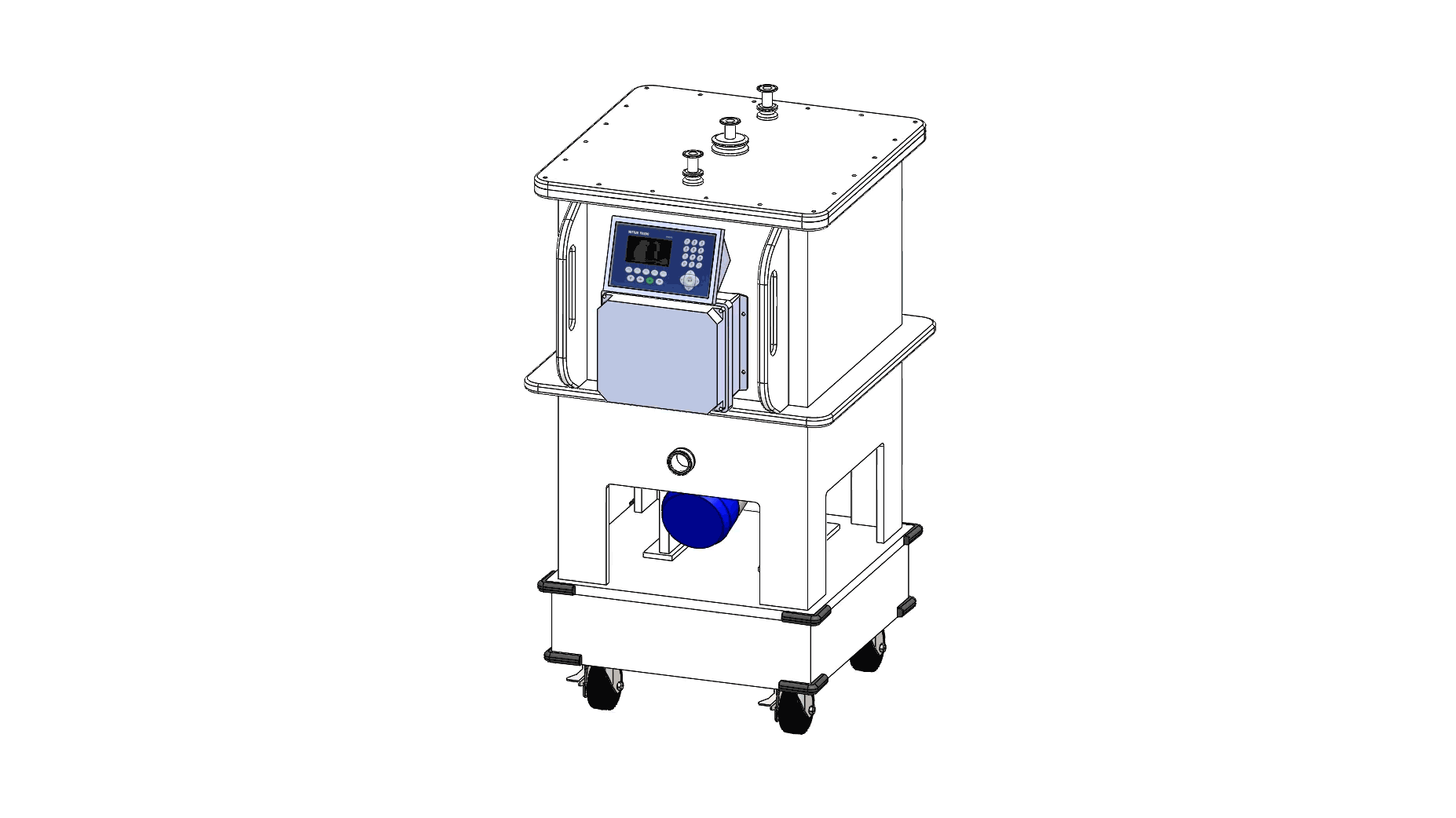
Gap Analysis:
Our case study begins in an older well-established precious metals plant that blends their finished product and then transfers this product into dozens of 55- and 300-gallon open top hold tanks. These tanks are stored on a rack (and on the floor in front of the rack) occupying approximately 600 square feet of manufacturing space. There are 3 different finished products across both size tanks. These hold tanks serve as bulk storage to be dispensed into a range of bottles to be shipped to their customers based on the order demands of the day.
An operator then works to fill orders by first identifying the proper bulk container. He then needs to maneuver a folk lift with a clamp device to pick up the bulk storage tank set it down on a scale located across the room. Once the operator verifies the bulk weight, the tank is again picked up by the forklift to be set below a mixer. At this point the mixer does not have the shaft and impeller installed to allow for room to set the tank in place below the mixer.
Once the tank is in place at the mixing station the operator manually installs the shaft and impeller into the mixer chuck and tightens it. Note: This operation is being done over the finished product. The product is then mixed to ensure a homogeneous suspension before dispensing finished product into the desired bottle sizes. After the mix is complete the operator has to disconnect the shaft and impeller from the mixer chuck, wipe it down and replace the shaft to a storage hook.
Once the mixing operation is complete the operator then lifts the tank to deliver it to a dispensing area near the scale. Finish packaging bottles are placed on the scale and filled through a pump with a hose through the open top tank. This process is repeated based on the number of bottles needed to fill that order or that days demand.
Once the dispensing process is complete, the operator again lifts the tanks with the forklift and returns it back to the bulk storage area. Because the finish product bottles range from 40 Kg – 300 kg bulk tanks get returned to the storage Area at various levels of fill. In other words, multiple bulk tanks with the same finish product start to pile up if not dispensed efficiently.
Once a bulk storage tank is empty, it is again transferred to another room to be cleaned out of place. This is a manually intensive process that involves the operator leaning into an open top tank to spray and rinse it out. It is a fairly messy and wet environment exposing the operator to less than desirable conditions.
This entire multi-step process is repeated for the various products throughout the day. As you can imagine there is a lot of room for improvement.
Observations:
- There are clearly a lot of steps in the process today. Moving tanks with a forklift from filling, to storage, to weighing, to dispensing, to mixing, to rinsing stations, etc. There are inherent safety problems moving tanks with the drum clamp extension across narrow travel areas. It is especially tight in the rinse station area.
- The clamps are damaging your tanks and pose a spill hazard. Open top tanks expose the operators to product. The product itself is subject to particulate contamination from the environment. Flat bottom tanks without a bottom valve are difficult to rinse out and handle, again exposing the operator to product exposure.
- Dropping drums onto the floor scale result in more frequent calibration and wear to the scale equipment. We expect there could be a loss in product or the potential to short fill a container.
- Top mount mixers introduce particulate contamination. Operators are exposed to product and rotating equipment. The same impeller size is being used for various size tanks. This may deliver less consistency in a homogeneous mix.
- There is a lot of room for organizational efficiency especially if you could store more tanks on the racking system. Open top tanks can be a bigger safety problem for overhead storage.
- There is quantifiable product loss during the weighing, pump out and rinse stages. This alone could deliver the ROI for this project.
Proposed Solution(s):
The Acuity Process Team worked closely with Management to explore the willingness to change and qualify the effort and expense to evaluate the right solution.
The Acuity process design team went to work integrating a comprehensive solution for a portable sealed top tank that was fully drainable and CIP able. This tank would allow for full drain ability out of a bottom valve. The portability removes the need for forklifts in this operation.
The design would include a seal-less, bottom mount mixer with a fully levitating design to ensure homogenous mixing to the last drop while dispensing. The seal-less design removes any potential for particle shedding. This design also removes operators from any exposure to rotating equipment.
Next, we incorporated an Alfa Laval Digital / Capacitive weighing system engineered to be the most robust weighing system for mobile applications. It handles the shock, side loading, and torsion problems associated with mobile equipment. The weighing system incorporates a digital display capable of controlling a pump to accurately dispense by weight. It delivers an accurate inventory of product within the tank. The system can collect data or communicate to your PLC through various protocols.
This system allows Management to complete the same process in a safer more accurate manner. It ensures better clean ability and reduces the risk of cross contamination. It removes several safety concerns from forklifts, rotating equipment, product exposure, and cleaning agent exposure. All of these factors reduce time and risk translating to more profitability and better employee retention.
Click below to learn more about how the Acuity Process team can help improve your process.
Leave a Reply
You must be logged in to post a comment.