Mixing and Blending is a fundamental part of many batch processes for a Life Science manufacturer. The Mixing of Buffers and Media preparations are needed daily. As many sites transition to more flexible manufacturing, accommodating smaller batches of different products can be challenging. The movement from large, traditional hard piped manufacturing plants that require Clean-in-Place (CIP) and Steam-in-Place (SIP) systems, to smaller Single Use manufacturing invites cleaning and storage challenges for process equipment. This is a potential solution for mixing buffers and media.
Traditional small batch mixing of buffers and media is often done in open-top tanks with a paddle or handheld top entry agitator. The open-top allows for the easy addition of powders that need to be mixed into solution. Polypropylene or HDPE plastic tanks are generally preferred for their resistance to chemicals and lower cost. This process can lead to dozens of tanks that have to be cleaned and stored. For smaller sites that do not have the utilities available or large washer systems, this can be a real problem.
Multiple solutions to be mixed simultaneously with the mixing station designs Acuity has built.
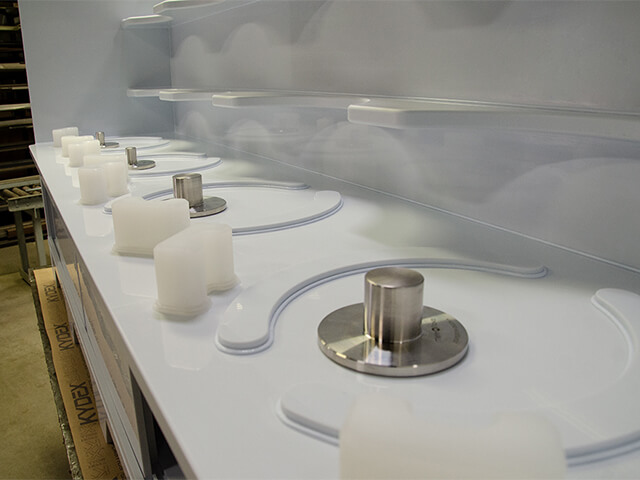
description

description
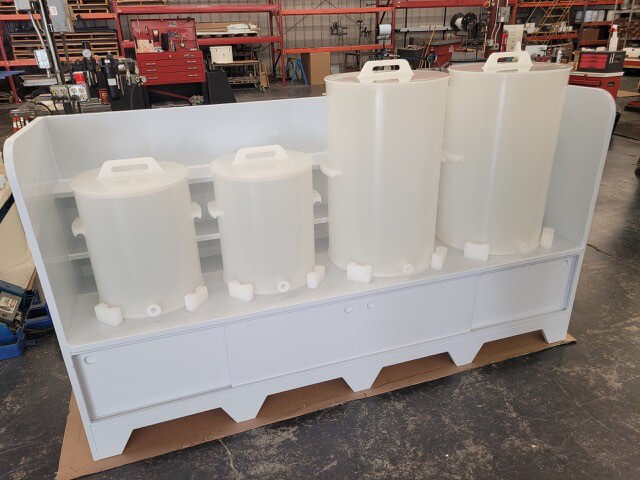
description
Let Acuity’s Process Solutions design team optimize your mixing process.
Features of Acuity’s innovative solution:
- Acuity’s’ Mix Station is an all Non-Metallic product contact solution.
- Our unique Cover removes the operator’s exposure to any rotating equipment.
- The mix tanks offer a closed or sealed cover to insulate your product from environmental contamination.
- All mechanical and power drive components are housed in an accessible cabinet below the mixing deck.
- The Tank body, Tank cover, Mixer weld plate and Impeller are available in Class VI natural polypropylene.
- Each tank is designed with a unique docking system to properly orient the weld plate on the drive unit.
- The Impeller is completely removable for easy inspection and cleaning. The tanks are designed with an optional side/bottom dispensing or dosing port.
- All tank Diameter to height ratios have been optimized to achieve a vortex if desired.
Whenever Sanitary mixing is required, consideration should be given to the advantages of bottom mount mixing vs. top mount mixing. If CIP or SIP systems are available, sealed tanks can be specified. Special consideration must be made to how the Top mount mixer’s rotating shaft will be sealed to avoid product contamination. In more manual applications, top mount mixing has disadvantages to installing and removing shafts and impellers. It can be difficult to adequately secure or fasten a top mount mixer to a plastic tank. Top mount
mixers have limitations in low volume mixing applications. This can be a challenge for products that need homogeneous mixing down to the last drop. Bottom mount mixing removes most of these concerns. Currently, bottom mount magnetic mixing is well proven and accepted in sanitary metallic tanks, and it has improved with the newer levitating impeller designs. To date, Mete Nova is the only bottom mount magnetic mixer company that expanded their offering with an all Polypropylene weld plate and impeller for Non-Metallic tanks.
Vortexing is a function of tank geometry, impeller RPM and viscosity of your product. A Vortex can be desired when trying to pull floating powders into solution. The proper vortex can pull powders all the way down to the impeller tip. If vortexing is problematic to your process, simply adjust your VFD to reduce the RPMs for less turbulent mixing.
Levitating mixing designs offer exceptional cleanability due to the available space for cleaning solution to flush between the levitating impeller and the guide bearing. Due to the frictionless, levitating design, the mixer can run dry for extended periods of time without generating particulate. This is the reason you can mix down to the last drop. This ability to mix at very low levels affords the site to reduce the total amount of tanks on site. For instance, you can mix 5 Liter – 40 Liter batches in a 30 gallon tank. Or, 10 Liters to 100 Liters. We offer a full range of sizes for small or large tanks. Acuity will work closely with Mete Nova to size and select the proper mixer for your application using a fluid dynamic modeling software.