Has your facility experienced safety concerns, bottlenecks, or other challenges while using a floor scale? If so, or if you rely on floor scales for your pharma or biopharma process application, adopting mobile-weighing solutions could be a game changer for your operations.
Transitioning from traditional fixed floor scales to innovative mobile weighing systems can deliver significant advantages, particularly for facilities looking to upgrade or optimize workflows. However, traditional resistance-sensing technologies, such as strain-gauge load cells, frequently do not satisfy the demanding performance criteria for mobile applications, historically restricting the functionality and effectiveness of mobile-weighing systems. Now, the advent of digital-capacitive load-cells marks a pivotal shift! Eilersen’s digital-capacitive load-cell technology, is the new standard for making mobile weighing a robust, reliable, and repeatable option.
Mobile Weighing Addresses Many Challenges Associated with Fixed Scales
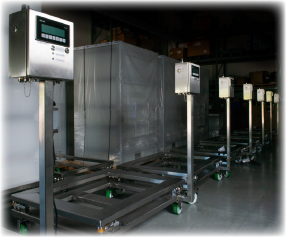
The use of fixed floor scales is common throughout the pharma and biopharma processing industries. However, they are associated with many challenges which can generally be addressed by the introduction of a mobile weighing system. Below are several examples of drawbacks/ limitations associated with fixed floor scales, highlighting how mobile weighing addresses these challenges.
Center of Gravity / Tip Calculations – When transporting equipment on to a fixed scale, the equipment needs to fit within the scale footprint. This can result in equipment such as bag carts, tank carts, etc. being taller and thinner than desired. Also, pushing equipment up and down the incline smoothly is required to avoid tipping or spills. On the other hand, a mobile weighing system does not have the same constraints in terms of spaitial dimensions and also does not need to be pushed up a scale incline.
Ergonomics – Moving heavy mobile systems onto and off of a floor scale incline can be a challenge (e.g. a 1000L tank / tote can weigh 2,500-3,000lbs.). The floor scale also adds height to the tank or tote making hook up or formulation additions more difficult. Incorporating a mobile weighing system into your process can eliminate these challenges altogether.
Flow Path Footprint – The flow path to push mobile equipment onto a scale and off to it’s next destination requires between 5X to 10X the floor space as compared to the required footprint of the equipment. In comparison, a 1000L tote with a digital-capacitive weighing system requires only it’s dimensional footprint, (approximately 25 sqft. of manufacturing floor space).
Operator Safety – Pushing heavy equipment (sometimes containing hazardous chemicals) onto and off of a scale can be a significant safety issue. Also, empty scales can be a trip hazard, while scales in operation require operators to stay off the scale and work outside the scale footprint. With the use of a mobile weighing system, the use of floor scales can often be greatly reduced or eliminated.
Process Workflow – Bottlenecking can be an issue for your process workflow when more than one piece of equipment has to wait for the scale to be free. Digital-capacitive weighing systems on mobile carts allow formulation wherever the equipment is located.
Inventory Monitoring – A digital-capacitive weighing system on mobile equipment delivers continuous, accurate, inventory monitoring capabilities while, with a floor scale, an operator must transport each vessel to the scale anytime a weight reading is required for inventory purposes.
Location, ID – With the AccuCart wireless transmitter option, tote inventories and locations can be easily managed.
Sustainability – Adding force tensioning brackets to support the Eilercal Force Calibration System option affords on-demand dry calibration, which eliminates the need for bags, water, or chemicals.
Control and Indication – The digital-capacitive system can send a signal to a valve, or pump for filling and dispensing applications. It can also be a reliable leak detection system.
In The Past – Strain-Gauge Load-Cell Technology
Regardless of the manufacturer, traditional weighing technologies are designed to measure the change in voltage across a sensitive element that is adhered directly to the load-cell body. Introducing load causes the load cell to deflect. In a strain-gauge load cell, the contacting strain-gauge element measures that deflection by changing shape. As the element changes shape the system recognizes a change in the return voltage across the system. Next, the change in voltage is translated to a weight measurement inside a summing box. The analog signal is then converted to digital introducing the potential for error.
For mobile-weighing equipment in the pharma and biopharma processing space, strain-gauge load cells have historically fallen short in terms of performance. Because the sensitive strain-gauge element is contacting the load cell, it sees all the overload, side load, shock, torsion, electrical noise, vibration, and potential stray current associated with the rigors of operation. For this reason, strain-gauge load cells can lead to frequent recalibrations, replacements, and downtime.
In summary, many engineers avoid specifying strain-gauge load cells on mobile equipment due to the downtime from out-of-calibration deviations. They revert to specifying a fixed-scale alternative to avoid mobile-weighing concerns. However, with the advent of digital-capacitive load-cell technology – reliable, robust, and accurate mobile weighing is now a reality for the pharma and biopharma process industries.
Digital-Capacitive Load Cells – The Only Choice for Mobile Weighing
Eilersen’s load cells operate via a completely different digital-capacitive technology. As load is added, Eilersen’s non-contacting capacitive sensor measures deflection by measuring the change in space between the capacitor and the load cell body. The sensor never sees shock, overload, sideload, vibration, electrical noise, or stray voltage.
The system is so robust it does not need any shipping blocks or additional mechanical torsion or overload bolts that you see on most strain-gauge systems. Each cell is factory calibrated and delivers a digital signal directly from the cell. This allows each cell to be addressable and visibly identified on the screen by serial number making diagnosis simple. The digital cables can be cut, shortened, or replaced without changing the load cell. In general, digital-capacitive load cells are not subject to the frequent recalibrations, replacements, and downtime that operators typically experience when using strain-gauge load cells.
Contact Acuity for a Pre-Engineered or Custom Mobile Weighing System
Acuity has extensive experience in process design and optimization for the pharmaceutical and bioprocessing industries. We commonly work with clients to provide tailored solutions that enhance safety and ergonomics, simplify their process, and maximize their footprint. It is generally very simple to upgrade SUT SUMs, SUBs, Totes, and Tanks that have problematic strain-gauge systems (or no existing weighing system). The Acuity Process Solutions team can help you size, select, and engineer the right weighing system for your process equipment. System set up, operation, and calibration support is also available.
Check out our weighing solutions page for a full line of Eilersen digital-capacitive load cells, AccuCart mobile weighing systems, the revolutionary new Eilercal calibration system, and other innovative products. Contact us today for a quote or to learn more.
Ted Haley – VP of Sales
Acuity Process Solutions
Leave a Reply
You must be logged in to post a comment.