Especially during a pandemic, few industries are more important to the nation than the pharmaceutical industry, which helps maintain the health and treat the illnesses of its citizenry. Justifiably, concerns about how a supply chain disruption might affect the industry are very high. Indeed, as the coronavirus grew and threatened factory operations in China, the FDA contacted more than 180 drug manufacturers asking them to evaluate their entire supply chain — including active pharmaceutical ingredients and other components manufactured in other parts of the world.
The pharmaceutical industry may be especially vulnerable to supply chain disruptions. Any delays or problems can result in potentially dangerous or deadly consequences for patients, a tragic outcome in itself that would be accompanied by possible insurmountable economic damage to the drug manufacturer. This risk of a supply chain disruption is often very difficult to mitigate, because components necessary to the industry are specifically approved for the manufacturing process of each drug — often making the substitution of alternative active pharmaceutical ingredients or equipment extremely difficult.
To expand on this, regulatory and safety constraints have kept the industry reliant on pre-approved materials and equipment. Thus, drug manufacturers are often locked into purchasing and using very specific components. For example, almost all active pharmaceutical ingredients are approved for use within a specific drug without acceptable substitutions. In addition, most of the equipment in a pharmaceutical facility is specified, tested, and validated through an extensive quality control reliability procedure conducted by trained qualified professionals. Understandably, the approval of alternatives is often time consuming and costly.
In light of these constraints, it is worthwhile to look at the aspects of production that are flexible enough to be managed as well as existing processes that can be tweaked to help support manufacturing.
How Will The Pharmaceutical Industry Adjust To Ensure Supply During Events Like The COVID-19 Pandemic?
Like so many of the nation’s industries, drug manufacturers are racing to find innovative ways to deal with the supply chain disruptions caused by COVID-19. Many pharmaceutical manufacturing sites have allowed their quality programs to accept “like in-kind” or “similar in-kind” replacements for obsolete equipment. In addition, many are working to approve a second vendor for sources of critical equipment and components, particularly those from areas or countries that are less likely to be disrupted by or are recovering from the coronavirus.
Another proactive action is conducting a thorough review of inventory minimum and maximum levels for reorder in order to hedge against stock outs. In addition, facilities managers and reliability engineers are reviewing their critical spares inventories to see how these components can be integrated into the manufacturing process as needed. In other cases, some manufacturing sites have invested and installed redundant systems that can be turned on instantly in the case of a breakdown, while others are considering manufacturing the same drugs at multiple sites.
Below are some of the proactive measures that drug manufacturers can take to help offset the risk associated with supply chain disruption.
Second Sourcing – Approving Alternate Suppliers/Manufacturers
A lack of time and resources are often the reason why manufacturers do not have alternate or second source vendors approved; it takes a great deal of time to audit and qualify vendors. However, under the coronavirus crisis, qualifying additional vendors to mitigate supply chain risks may be a worthwhile business investment. In some cases, the replacement products may not be identical; however, products with the same fit, form, and function may be effective enough to reduce supply chain disruption risk.
Re-Evaluating On-Site Inventory Systems
The COVID-19 pandemic has raised concerns over the confidence of current inventory management systems. Supply chain inventory levels are calculated using expected availability and delivery lead time to fill demand without an interruption in supply; however, the typical minimum/maximum reorder points may no longer be valid during the current crisis.
There is a delicate balance between inventory demand and available inventory space (especially high-priced GMP warehouse space). Chain of custody quality controls limit local distributors’ ability to store inventory for their customers. Manufacturers can pursue solutions to this problem by assessing how to effectively and innovatively store more production material in the GMP space through custom storage solutions and transfer carts.
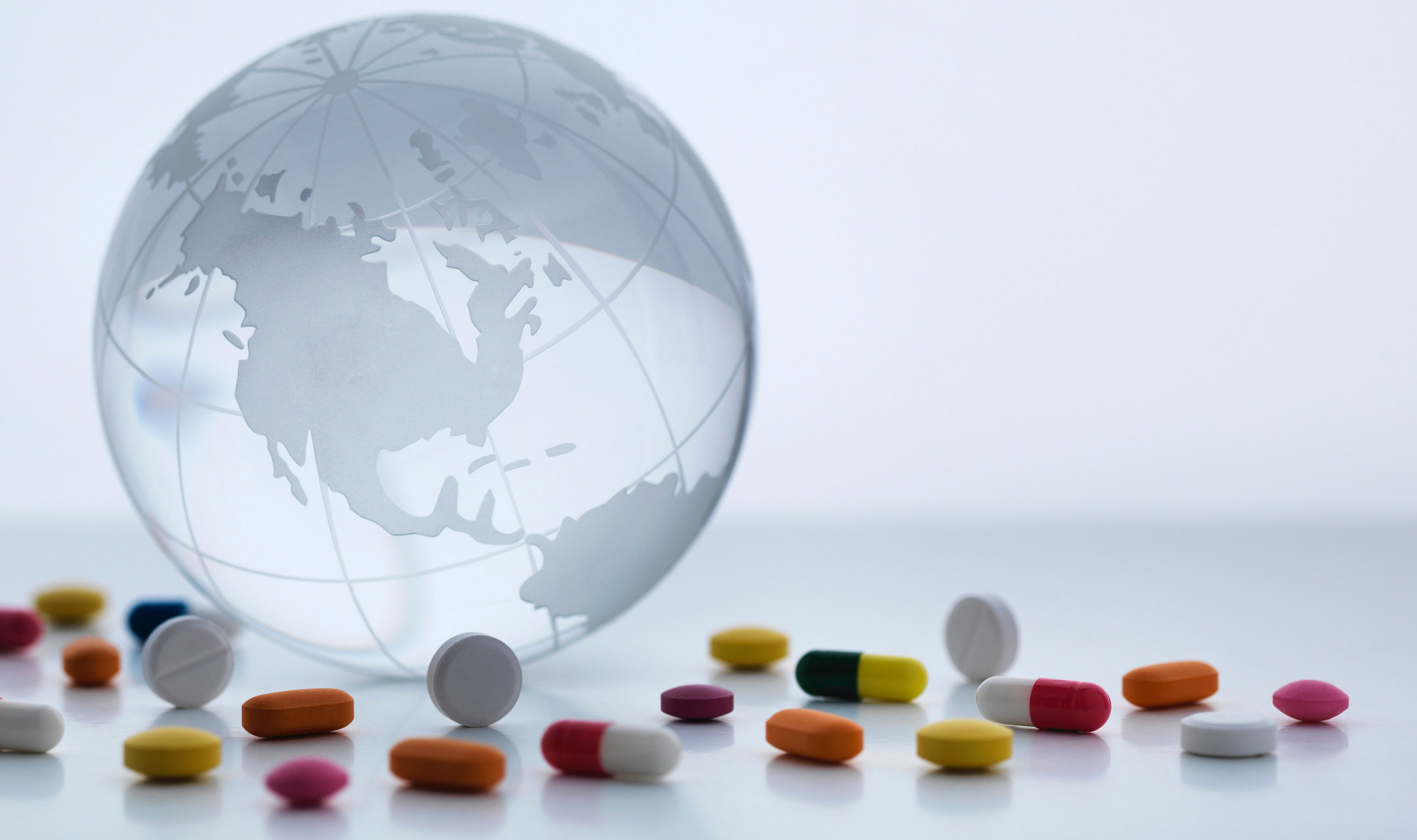
Re-Evaluating Critical Spares
Critical spares are composed of redundant equipment and or parts to maintain and rebuild existing equipment. An effective critical spares program results in zero downtime because once equipment has malfunctioned, a back-up part or piece of equipment can be easily pulled to seamlessly get the manufacturing process back on track.
A proper critical spares analysis should be an ongoing task involving taking account of the critical care inventory and creating a timeframe of needed lead times; however, it is often overlooked due to a lack of resources. Evaluating the spares inventory during the present crisis can be a valuable tool in reducing the risk of supply chain interruption as well as creating a positive process for post-pandemic drug manufacturing.
Acuity Process Solutions Has The Expertise To Help Get You Through This Stressful Time
The global pandemic has introduced a challenge at a level never seen before in modern manufacturing. Luckily, Acuity Process Solution has years of experience in the industry and in adapting to the flows and ebbs of supply, demand, and technological evolution. Acuity is currently available to discuss ways to reduce the supply chain challenges in the life science industries and is willing to explore new and innovative ideas to shape our service and capabilities to meet the changing environment under COVID-19.
Leave a Reply
You must be logged in to post a comment.