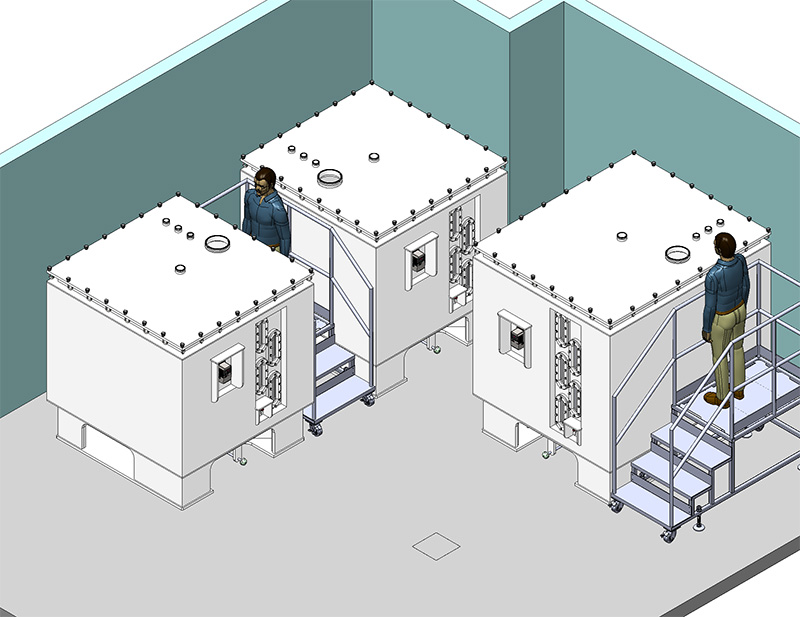
Problem:
A local Oligonucleotide manufacturing facility needed to expand their buffer capacity to meet increasing demand. The request was to increase the existing 500 liter and 1000 liter buffer mix/hold tanks capacity to 3000 liter and 4500 liters respectively. A buffer capacity upgrade of this volume was a significant challenge based on the available space in the existing suites, low ceiling heights, and existing doors and hallway dimensions. These existing dimensional constraints immediately ruled out the ability to use a conventional cylindrical mix tank design. The low ceiling heights and the site’s desire to stick with conventional top mounted mixers presented dimensional and structural support challenges. The low ceiling heights also squatted the tanks down to a less than optimal height to diameter mixing ratio. Lastly, the process required 10-30 doses of 12 Kgs of salt minerals to be manually dosed into the tank through a top mounted port. The minimum space above the tank to complete the manual dosing needed to be at least 24”.
Design Considerations
The Acuity Process Solutions design team worked closely with the end user to prioritize their current user required specifications for mixing buffers.
- The materials of construction had to be USP Class VI Polypropylene.
- All Elastomers and wetted surface are to meet USP Class VI certification
- The tanks needed to be CIP able.
- Dosing of 12 Kg salt needed to be ergonomically optimal for the Operators.
- Sight Glasses and graduations for visual level verification
- Mixers were to be controlled by Variable Frequency Drives
- All platforms need to be portable with fixed leveling feet. M.O.C. 316 SS construction
- Polypropylene Radial Diaphragm tank outlet valve
- Top Mount Agitators and impellers were to be like the existing buffer for repeatability
The first step was to model the suite and review the proposed locations for all 3 tanks. It was clear that cylindrical tanks would not be optimal for mixing. Given the batch size, the low ceiling heights would force the tank height to diameter ratios out of optimal mixing ratios. We decided to explore non-traditional square mix tanks as an option.
The operators needed a minimum of 2 feet of clearance above the tanks to facilitate multiple 10-12 Kg -manual doses of salt additions. Given the existing 9 foot ceilings, and the requirement for 2 feet of clearance for process dosing operations resulted in a Max tank height of 7 feet. This max height of 7 feet was the starting point to determine the final tank geometries. Our goal was to design a square tank but the existing door openings forced the final design to be slightly rectangular.
Acuity Process challenged the top mount mixer specification by introducing a Mete Nova polypropylene bottom mount mag drive mixer. The bottom mount mag mixer removed the need for structural support of a large mixer, motor, and gearbox above a nonmetallic tank. It also removed the difficulties of installing a large shaft without removing the tank cover. And it removed the safety concerns for maintenance personnel to work on top of the tanks. Bottom Mount mixing technology for buffers had been well proven in cylindrical tanks and was in wide use across the Life Science industry.

Given that the salt minerals were heavier than water the low-level pumping action of the Mete Nova Mag drive mixer would conceivably shorten batch mix times. The corners of a square tank act as half baffles aiding in the ability to mix efficiently. The outward sweeping of the Mete Nova Mixer would also help avoid salt particles settling. Acuity Process also designed welded fillers in each corner to minimize dead zones in the corners. Mete Nova made recommendations for the mixer to be located as close to the tank bottom valve located in the center of the tank. The tank floor was sloped in a pyramid style to the tank bottom valve to enhance drain and mix ability.
The biggest advantage of the bottom mount mag mixer is the ability to mix small to large batch sizes ranging from 0-4500 Liters.
From a safety standpoint, the bottom mount mixer motor & gearbox were easily accessible. Mete Nova’s integral lowering device option was selected to disengage the drive magnet with a simple turn of the hand wheel. This avoids the need to remove or disassemble the drive unit.
Acuity Process also designed in custom sight glasses. These sight glasses were staggered to improve the structural integrity of the side wall. The mixer variable speed drive is located within reach of the sight glasses so an operator can verify flow, level, and CIP as needed. A zero dead leg sample port was also fabricated and installed at a low point just below the sight glasses.
The cover gasket groove included and sloped V-Groove to allow CIP fluid coverage and drain ability.
Custom stainless steel ladder platforms were designed at optimal height for an operator to dose into and access tank ports. All ports were located within reach of the platform decks to enhance ergonomics.
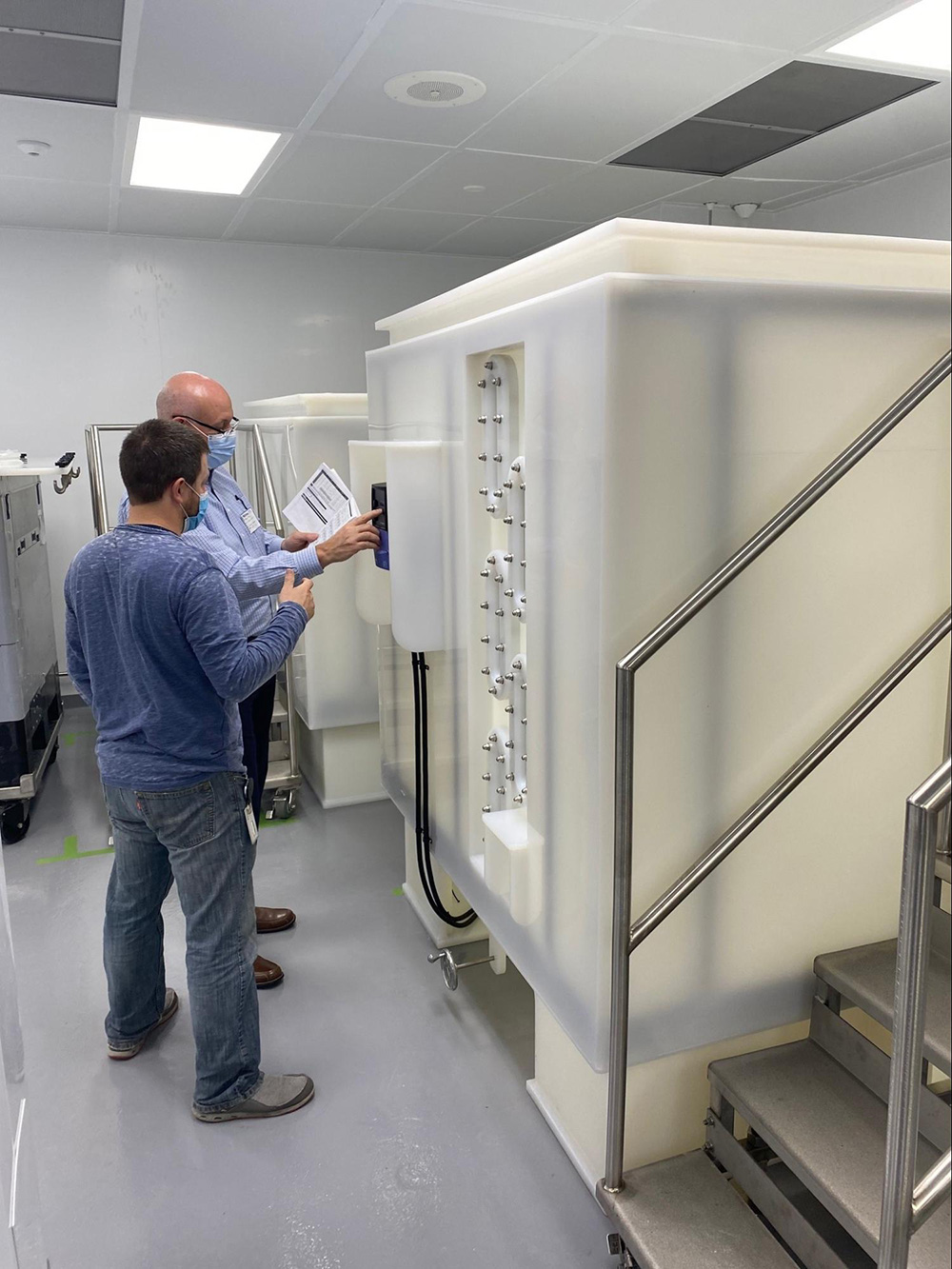
Big Problem, Simplified
In summary the square tank design delivered approximately 33% more buffer hold capacity in the same usable footprint. The square tank design delivered fast, repeatable, homogeneous mixing. The Polypropylene bottom mount Mete Nova Mixer delivers flexibility from small to large batch sizes across the full range of the tank. The innovative sight glass arrangement offers visual verification on level and the entire dosing to mixing process can be verified. The platforms are all 316 SS using SlipNot metal safety flooring. Moving the mixer from the top to the bottom of the tank improved the site’s safety objects and made life a bit easier for preventative maintenance technicians.
We would like to acknowledge the Mete Nova support team for their contribution and suggestions throughout the design and commissioning process. Most importantly we would like to thank our end user Process Engineering team. Their contribution and willingness to collaborate throughout the process resulted in an innovative, robust design that works.
Please consider engaging Acuity Process Solutions for your next process design challenge.
Leave a Reply
You must be logged in to post a comment.